History
In 1962 at 20 years of age, Campbell Bolwell transformed his hobby of building special sportscars into a business. Developing hands-on skills in fibreglass moulds and moulding techniques his first commercial model, the Bolwell Mk.4, sold over 80 units and is testimony to entrepreneurial flair and dedication to a dream.
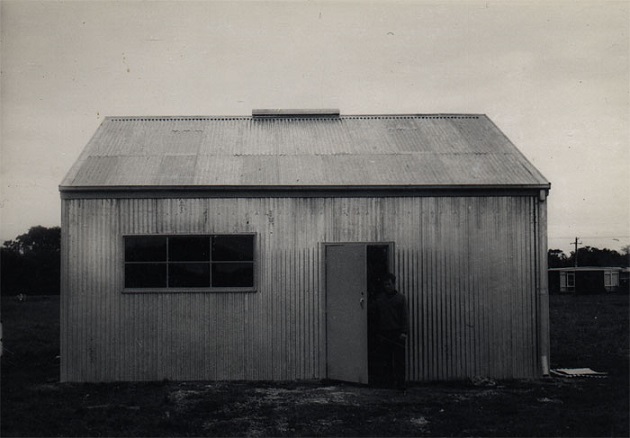
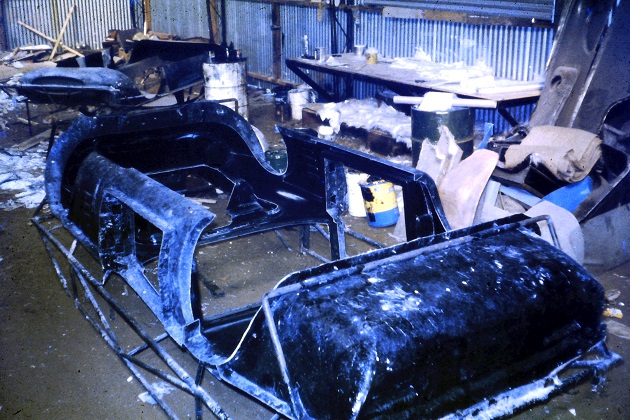
The Mk.4 was clearly aimed at motoring enthusiasts with little money but with some mechanical knowledge and unbridled enthusiasm. Design influences for the Mk.4 included the Elfin Streamliner, the Lotus 11, and the Maserati Birdcage, the latter so named because of its intricate tubular spaceframe chassis. The Mk.4 spaceframe chassis was unusual for its’ time in that it only used two chassis compartments where traditionally there were three: the engine; the cockpit to the scuttle; and the cockpit to the back; and the suspension was hung off the back and the front. Bolwell’s chassis had the driver’s feet pushed through the main bulkhead and the engine moved right back to the offside of the driver’s legs to get better weight distribution, more like a rear-engined car.
The more commercial Mk.5 followed the Mk.4 demonstrating that Bolwell Cars had made the transition from a backyard business to a serious specialist vehicle manufacturer. The Mk.5 incorporated new design and manufacturing concepts as well as new marketing ideas, being variously advertised as “It only looks expensive”, “…this car does not cost ₤3,441!” and “A device for making dreams come true”. The Mk.5 appealed to a much larger audience who were seeking options for a Holden 6, which were plentiful at the time. In keeping with Campbell Bolwell’s sports car design theories, the chassis was designed so that the engine was mounted well back from the front cross member in order to improve front/rear weight
distribution.
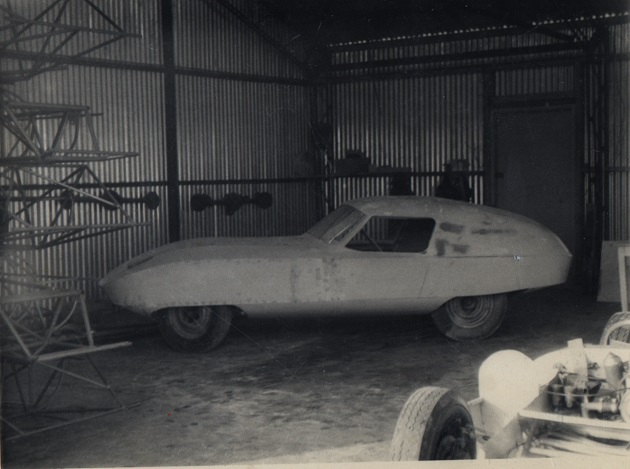
The one-and-only SR6 was created to support the advancement of Bolwell Cars into serious motor racing and was the first Bolwell with a mid-mounted engine. The SR6 was designed in conjunction with and for a well-known local sports racing car driver (Alan Newton) and remained the one-and-only due to the cost and complexity of the build. The SR6 is still being raced to this day.
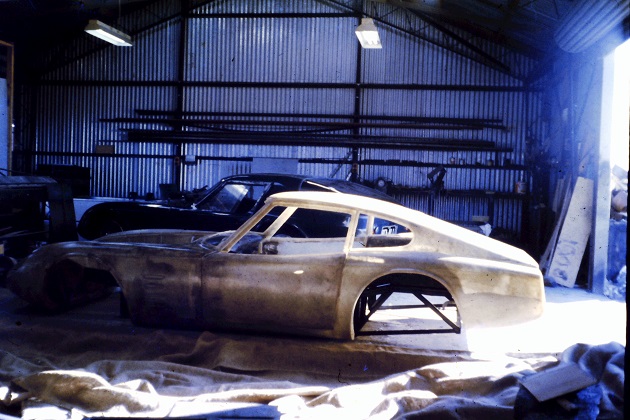
Design work started on the Mk.7 in 1965 with the car being featured on the front cover of Sports Car World in March 1967. The Mk.7 was more refined than the Mk.5 and was largely designed around Holden components which appealed to the market. They were sold in various kits forms with improvements progressively incorporated into the design. Approximately 400 units received registration plates, making Bolwell Australia’s fifth largest vehicle manufacturer of the time.
The Bolwell Mk.8 was the first model to receive its’ own name – the “Nagari”, believed to be an Aboriginal word meaning ‘flowing’. Conceived and mostly produced as a fully built production car, Bolwell Cars was now able to manage and deliver consistent quality. The Nagari was designed to incorporate Ford components and included a V8 engine, and was available with either a Coupe or Sports body. The Nagari benefited from Campbell’s brother Graeme Bolwell’s working holiday in the U.K. which included a stint working at Lotus in late 1966: Graeme came home with plenty of inspiration about what could be done with fibreglass and the need to design for the material being used which meant that the Nagari was designed purely for fiberglass.
Nagari production continued through to 1974 when a number of factors came into play to effect the demise of Bolwell Cars at this time, including rising oil prices and the impending stricter ADRs (Australian Design Rules). The new safety standards required a new car to be crashed into a concrete block for test purposes, which was not an economic proposition for a small manufacturer producing less than 100 cars a year, so the party was over.
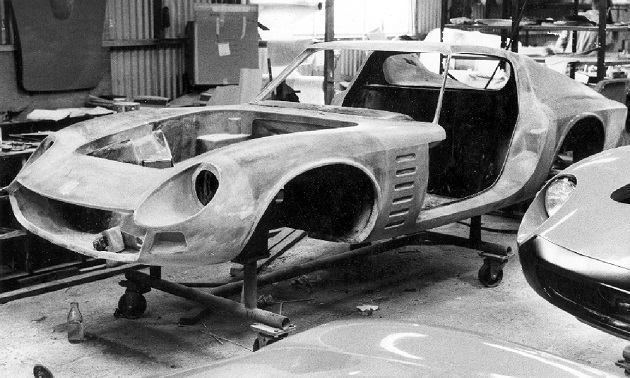
The Bolwell expertise in fibreglass manufacturing techniques and production enabled the company to begin designing and producing a wide range of other fibreglass products, from small vehicle components to ocean going yachts. Graeme’s main interest had been in cars, and he left the business with Campbell remaining in charge. The Bolwell Corporation evolved to deliver commitment to great design, ongoing innovation, state-of-the-art manufacturing processes and seamless delivery and continues to this day.
In 1978, the Bolwell engineering and design team set out to create a new sports car that was fun to drive without any of the compromises of the motor industry’s safe, conventional and boring suburban “committee car”. The ‘Ikara’ was to be sold as a kit or component car as this was the best way for Bolwell to be able to offer the Ikara at anything like an affordable price and without the requirement for Bolwell, as manufacturer, to go through all the ADR testing compliance and regulations that had effectively killed the Nagari.
The Ikara was also used by the (now named) Bolwell Corporation as a way to promote its’ expertise in fiberglass and composites. Because of its marketing emphasis, the finish of the Ikara fibreglass panels and general workmanship was top class; a view confirmed by magazine and newspaper car reviewers almost without exception. As a result, Bolwell Corporation attracted several lucrative corporate contracts to design and produce various fiberglass components.
In the early 2000’s, Campbell Bolwell once again ventured into the design of a new Bolwell – the Nagari 300. The idea for the Nagari 300 took place in Canada using some of the infusion technology developed during a period that Bolwell were building wind turbine blades there: the first design sketch was drawn on the back of a serviette whilst dining in the local ‘Tim Hortons’ donut and coffee restaurant. The technology behind the Nagari 300 (Mk.10) was based on light weight: Bolwell’s extensive experience in composites and using the new infusion technique enabled it to design a lightweight structure with high strength. The 300 would demonstrate this technology.
The Nagari 300 included a Toyota 3.5ltr V6 mid-mounted engine with weight distribution biased to the rear. The basic structure was based on a torsional rigid occupant capsule which incorporated various materials such as carbon fibre and Kevlar as well as glass fibre. The infusion process kept the weight down without compromise to the strength. After taking almost 4 years to approve the 80+ ADRs, compliance was finally achieved but sales had disappeared because of the delay. Only a handful have been built to date.
The Nagari 500 originated when it was discovered that the Nagari 300 concept and design could fit a V8 engine in place of the V6 with very little modification. With small modification to the exhaust system, power was close to 500bhp (hence the description ‘Nagari 500’). The Nagari 500 has some styling changes from the 300 but remains essentially a mid-engine vehicle with a classic shape and sophisticated interior.
Wheelbase needed only an increase of 50mm and there was sufficient room for the Chevrolet LS3 motor even if the standard supercharger was mounted atop. Further sophistication to the capsule design and the use of Corvette forged alloy suspension arms meant that weight could be controlled and the final vehicle weighed in at 985 Kg. Unofficially the Nagari 500 will achieve a 0 to 100Kph in under 3 seconds.
The Nagari 500 was released at MotorClassica in Melbourne in 2019 at the Melbourne Exhibition Building for the 50th anniversary of the Nagari. The original Nagari was released exactly 50 years previously at the same building. The development team consisted of Toby Hunt (Bolwell Technology P/L Chief Development Engineer), Graeme Bolwell, and Ross McConnell, noting that it was Graeme and Ross who worked together on the original Nagari 50 years previously after Graeme returned from working in the UK with Colin Chapman at Lotus. History was repeating itself.
Bolwell Cars has earned a unique place in Australian automotive history for the Bolwell marque.